What is Electraulic™ Actuation?
Electraulic™ Actuation is a brand of electro-hydraulic actuation unique to REXA. It combines the simplicity of electric operation, the power of hydraulics, the reliability of solid state electronics, and the flexibility of user-configured control.
Electraulic™ Actuation consists of two major components: the mechanical sub-assembly and the electrical sub-assembly. Each component plays a critical role in combining the benefits of major actuator types (pneumatic, electric, hydraulic) while eliminating the drawbacks of each technology. The foundation of our technology is the patented breakthrough in hydraulic circuitry called the Flow Matching Valve System. In conjunction with a bi-directional gear pump coupled to either a DC stepper or AC servo motor, this system is a highly efficient method of moving hydraulic fluid from one side of a double-acting cylinder to the other.
At REXA, we provide both Linear and Rotary actuators, as well as Damper Drives, depending on your application.
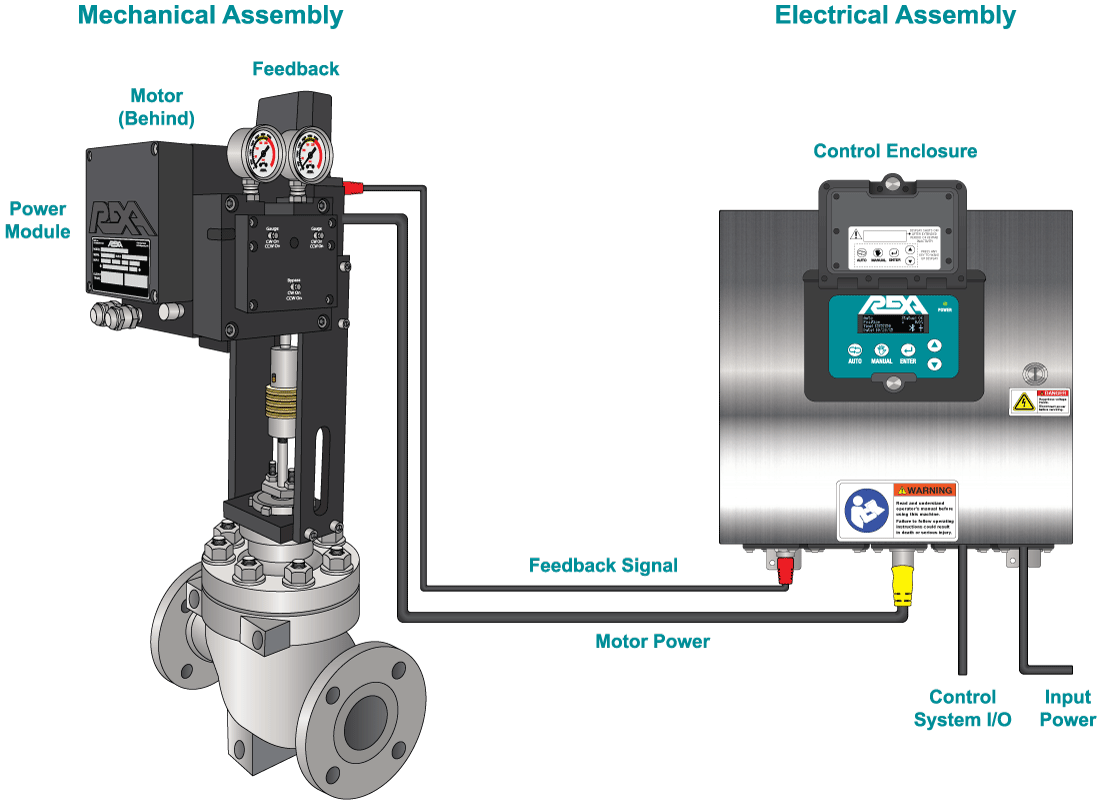
How it Works
While monitoring travel and signal ranges set during calibration, the CPU converts the incoming control signal into a target position. An active feedback sensor directly mounted to one end of the cylinder output shaft determines the actuator’s current position. The difference between the target and the current position interprets as an error (deviation). If the error exceeds the user-programmed deadband, the CPU will initiate corrective action by starting the motor.
A bi-directional gear pump, driven by the motor, generates the necessary pressure to overcome the process conditions (see graphic below). System oil travels from the pump through a series of pilot operated check valves, known as the Flow Matching Valves (FMV’s). The FMV’s manage the transfer of oil out of one side of the cylinder and into the other. This transfer of oil drives the actuator to the target position. Once the system determines the actuator is at the target position, the motor and pump stop and the FMV’s close (seat). The FMV seating then hydraulically locks the cylinder in place. The motor will only turn on again if the incoming control signal changes. Motor operation is not required to maintain the actuator’s position.