Project Description
Water Pumping Background
Reliable access to drinking water is an overlooked necessity to the modern world. When using pump stations, it is critical to ensure full capacity is always readily available. Standard design practices were created to promote reliable operation, but the technology available has not always been up to the task.
Valve actuation on the discharge side of a pump requires careful consideration. Reliability is critical to ensure full water pumping capacity, especially during high demand periods. Equally important is for any discharge valve actuator to provide a guaranteed fail-safe system to protect the pumps in the event of an emergency (when applicable).
Why do other actuation technologies come up short in this application?
Water often gets pumped across long distances and elevated terrain. Any failure or emergency condition that halts active pumping can result in a flow reversal where gravity forces the flow back down the line towards the pump. This causes the pump to spin backwards. To prevent this, there is typically a check valve on the discharge side of the pump installation. In some cases, a check valve may be combined with an actuator to serve as both the in-line check and control valve package.
Commonly used actuator technologies do not represent the most reliable options available and typically require frequent maintenance. A need exists for a more reliable alternative that requires lower cost of ownership.
Pneumatic-based systems employ a central compressor system that generates air pressure fed to multiple pneumatic cylinders driving valves. Air is a compressible medium, so it is not a rigid form of actuation. As such, pneumatic actuators are susceptible to “sticking” and “sliding” (also known as deadtime and overshoot), resulting in poor response and control.
Hydraulics also present a new set of concerns regarding the oil medium itself. In any hydraulic system, roughly 80% of all failures are attributed to the breakdown of oil. Maintaining oil within these systems is of critical importance. Hydraulic actuators require periodic oil changes, as well as a method of filtering that also requires periodic attention. This task can be quite burdensome in larger pumping stations where massive volumes of oil may be required in these systems.
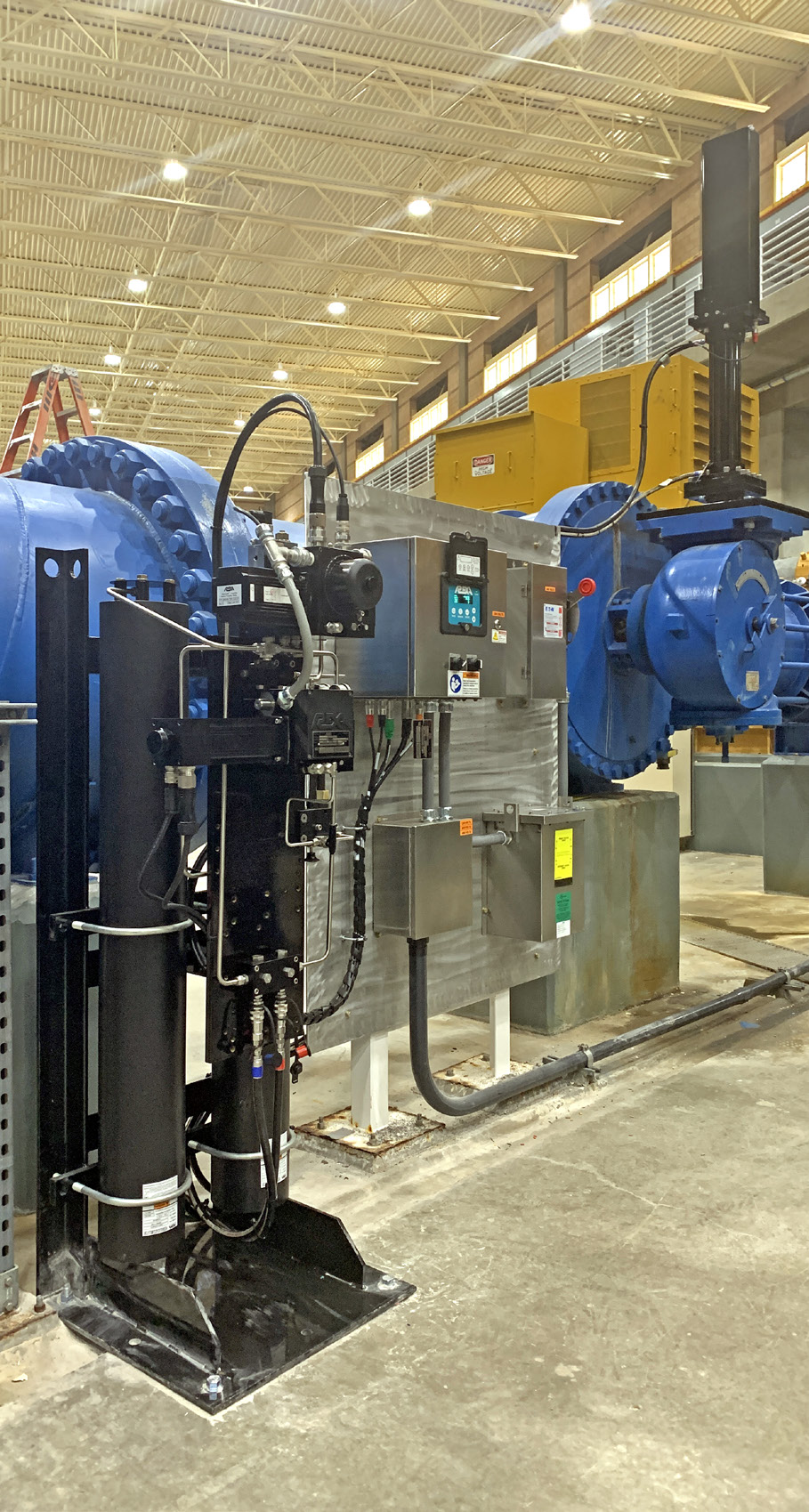
The REXA Solution
REXA offers the most reliable actuator solution for a pump discharge valve service. Individual actuators are supplied for each pump discharge valve, eliminating the single point failure hazard posed by centralized systems. REXA delivers smooth and controlled pump discharge valve operation during both normal and emergency conditions. Any speed requirements can be met to maintain a pump curve while also eliminating water hammer / surges that can damage piping infrastructure. REXA is the most energy efficient actuator available, reducing your power costs. With dramatically reduced oil volumes compared to traditional hydraulic systems, REXA eliminates any environmental contamination or insurance related concerns.