Coke oven main pressure control is a critical control application for the safe operation of coke making. A plant’s actuator not only must position the cross-over valve to achieve a pressure of 12 +/- 1 mmWC, but it also must avoid pressure spikes from volatile gases soon after coal charging, as shown in Figure 1. If the actuator is slow to respond, the collection main and coke oven gas pressure will increase and leak toxic gas at the oven doors. If the actuator overshoots, the coke oven pressure can decrease to a vacuum, entraining oxygen in air which ignites in the oven. Both pressure scenarios present major safety concerns.
During normal operation, the cross-over valve becomes coated in tar originating from the coke oven gases. Tar build-up increases the required torque to turn the valve. Left unchecked, this condition can potentially damage the valve, causing unnecessary downtime to repair. Regular cleaning ensures proper valve operation. Therefore, plant operators and technicians prefer to optimize the cleaning schedule.
Why Upgrade to REXA?
The preventative maintenance schedule for cleaning the cross-over valve at a major integrated mill in Canada was based on fixed time intervals without any data related to its condition. The mill recently retrofit the existing valve with a REXA Rotary Electraulic™ actuator including the diagnostic capability to monitor
operating pressure. The previous actuator’s oil reservoir was open to the environment, requiring frequent scheduled oil changes. The actuator also used a mechanical linkage to actuate the valve stem. These linkage assemblies introduce hysteresis, which can worsen over time and ultimately lead to poor control.
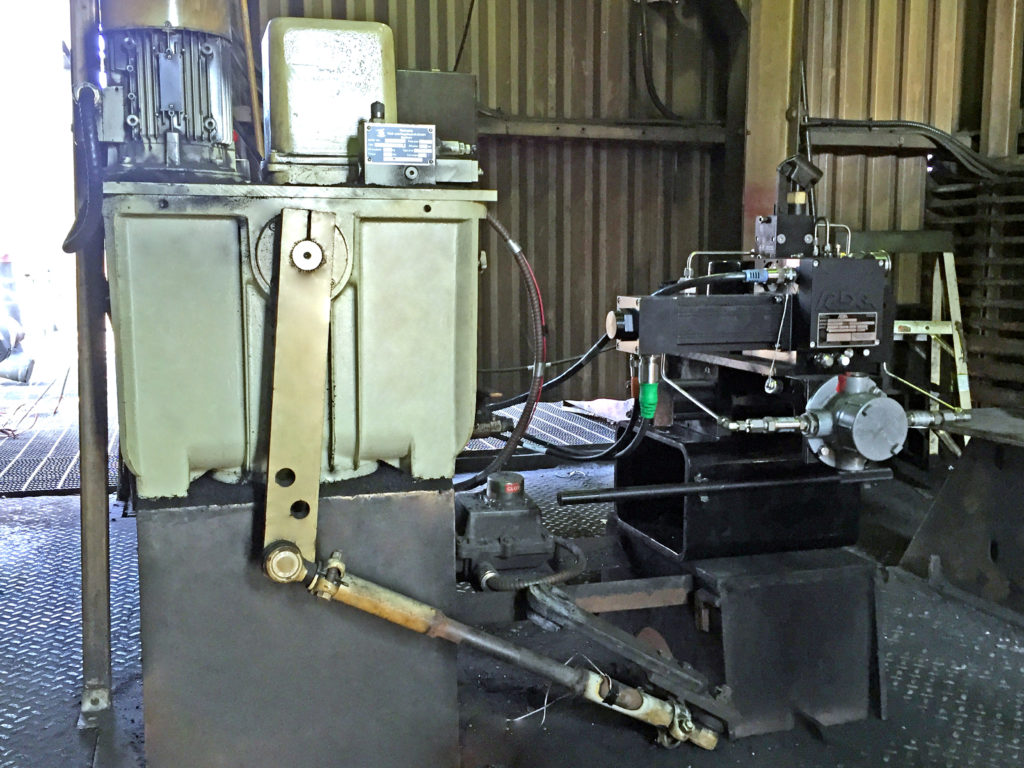
Before
A REXA Success
REXA consulted plant personnel and developed a solution which eliminated the need for mechanical linkage assemblies by mounting directly to the valve stem. With accuracy to 0.1% of desired position, less than 70mS deadtime, and zero overshoot, the collection main pressure control began operating better than ever before. The self-contained, positive pressure, non-vented Electraulic™ system never communicates with atmosphere, improving reliability and eliminating routine fluid maintenance.
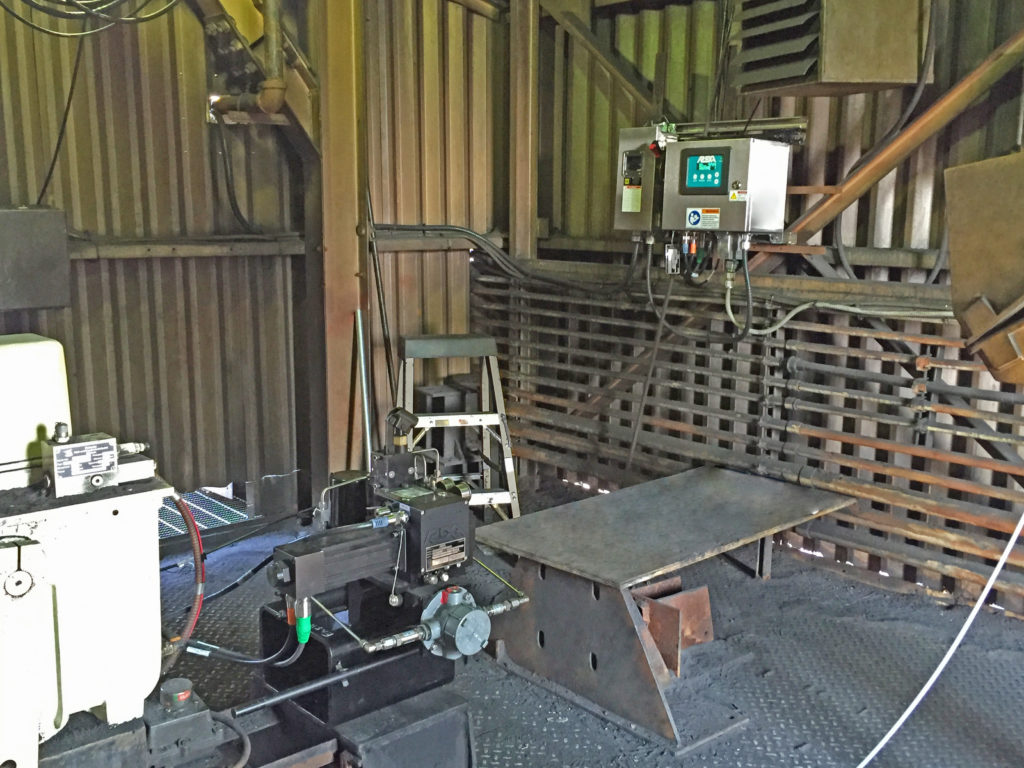
After
Our Bluetooth® graphical user interface tool displays the operating pressure and records it over time. Userconfigurable warning and alarm limits let our customer know when a pressure threshold is reached – signaling a need to initiate the valve preventative maintenance cleaning procedure. This ensures the maintenance group can schedule the cross-over valve cleaning at an interval based on the valve’s health instead of an arbitrary time. Cleaning the valve only when necessary enabled a reduction in cleaning frequency, increasing uptime and personnel safety. Unscheduled shutdowns due to tar build-up on the cross-over valve were eliminated.
Download the full Success Story & Learn More
Click the button below to download the full success story! Interested in learning more about our solution for other applications in the mining industry? Click here to further explore REXA in other applications.