Hydroelectric Power Plants: What is a Reaction Turbine?
Hydroelectric power is a reliable renewable energy source accounting for roughly 17% of the world’s energy. With countries around the world actively expanding capacity or looking to do so in the near future, hydropower will continue to play a key role in the rise of renewable energy production. Hydroelectric power plants utilize two main types of turbines: impulse and reaction.
REXA recently retrofit Electraulic™ Actuators on two DN600 bypass valves used on a Kaplan-type reaction turbine for a hydroelectric power plant in Poland! Reaction turbines are generally used for plants with lower head and higher flows. They utilize the hydrokinetic energy of moving water to create electricity. Water (usually isolated from ambient pressure inside a penstock) moves through to the turbine, increasing in pressure as it reaches it. This allows the flow of water to rotate the turbine runner. Bypass valves play an important role allowing continuous operation in case equipment damage or failure occurs. Unstable performance of these valves creates both inefficient and potentially dangerous operating conditions.
Why Upgrade to REXA?
Before the REXA retrofit, this hydroelectric plant was unable to operate above 40% of its rated output. The previously installed double-acting pneumatic actuators were unable to deliver the stable control necessary for startup and to operate near the plant’s limit. Air compressibility and static friction led to overshooting and a continuous hunting for target setpoint. The pneumatic performance limits ultimately forced the plant to reduce output in favor of safe and stable operation.
Specific requirements for this application included the ability for actuators to be adapted to the existing eccentric-type metal butterfly valves, to close normally, and to be equipped with a fail-open feature all while adhering to a limited space with only small changes allowed. Slow and steady actuation is imperative to control water flow and prevent potential water hammer. With this in mind, the plant required actuators to close in approximately 40-60 sec 1-speed (with time adjusted onsite) and open in approximately 2-6 sec 2-speed (slow phase #1, followed by fast phase #2 with time and length of each phase adjusted onsite). Finally, the supplied voltage requirements would be 24VDC or 1-h230VAC.
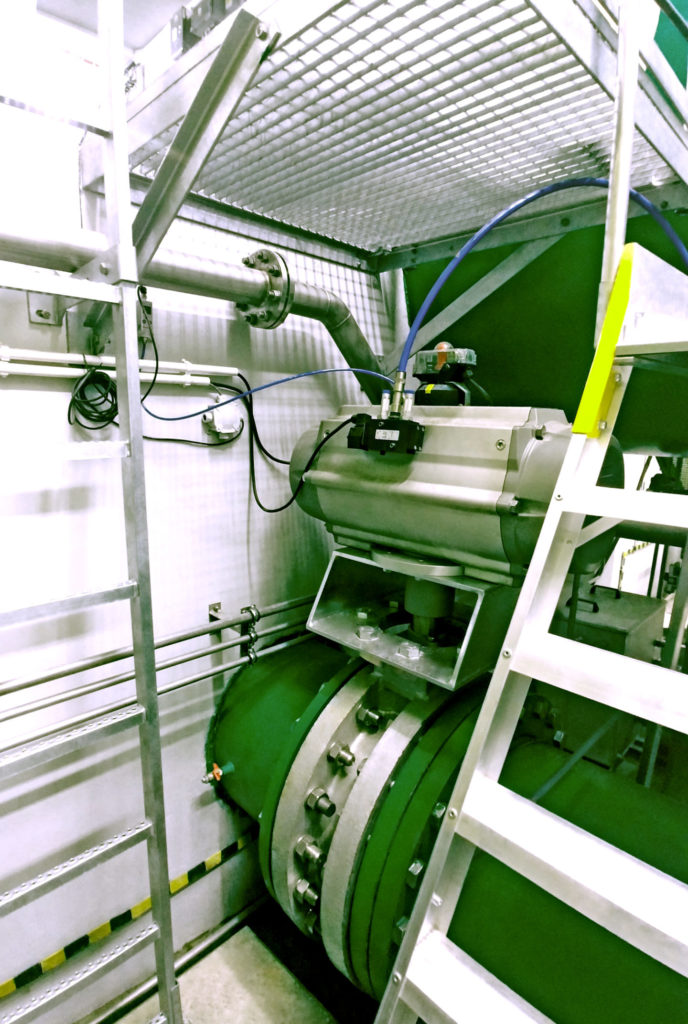
Before
A REXA Success
After meeting with plant personnel, REXA developed a customer-specific solution addressing their pain points. According to the above requirements, the right solution included two rotary actuators with an extensive range of on-site fine tuning features and a smart use of the break surge point option (unique to REXA). After final tuning, this retrofit allowed the plant to finally (and safely) reach 100% capacity. Furthermore, using REXA Electraulic™ actuators saved the plant costly mechanical/construction changes and shortened total project time!
Download the full Success Story & Learn More
Click the button below to download the full success story! Interested in learning more about our solution for other applications in the Hydroelectric power industry? Click here to further explore REXA in other applications.
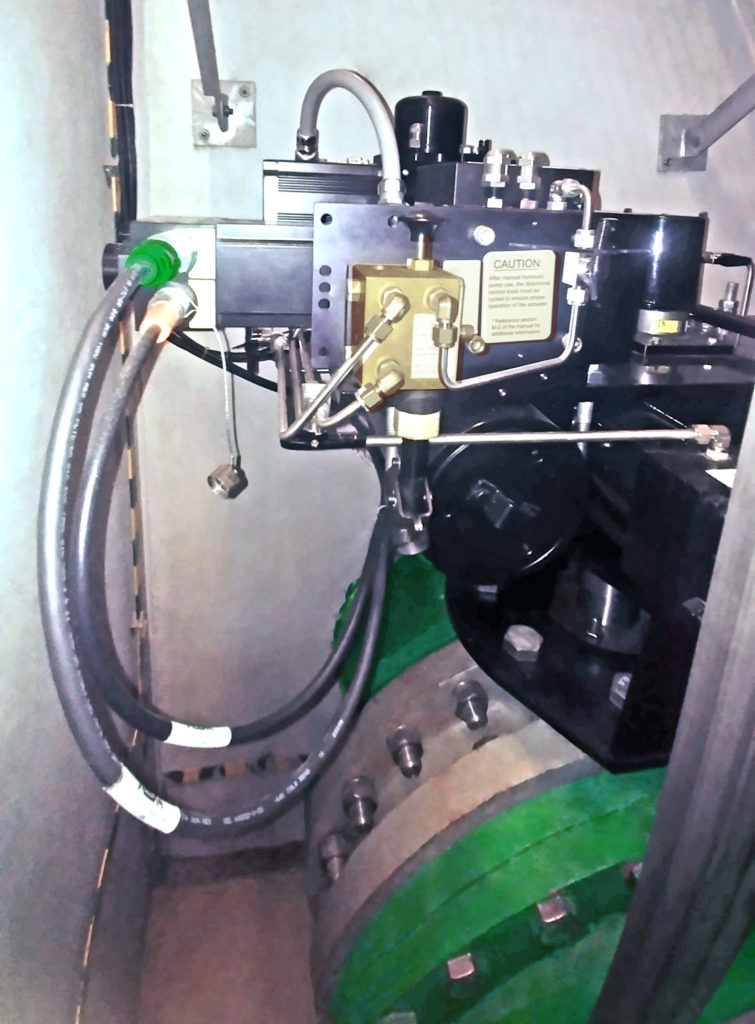