Steel companies around the world continuously introduce and enhance processes that emphasize sustainable development. Key sustainable targets include minimizing the environmental footprint and increasing energy efficiency. These companies proactively develop actions to decrease fossil fuel consumption, thus reducing greenhouse gas emissions. Through all these initiatives, companies provide it is possible to be socially responsible while reducing operational cost to produce quality steel.
Modern continuous rolling mills produce large quantities
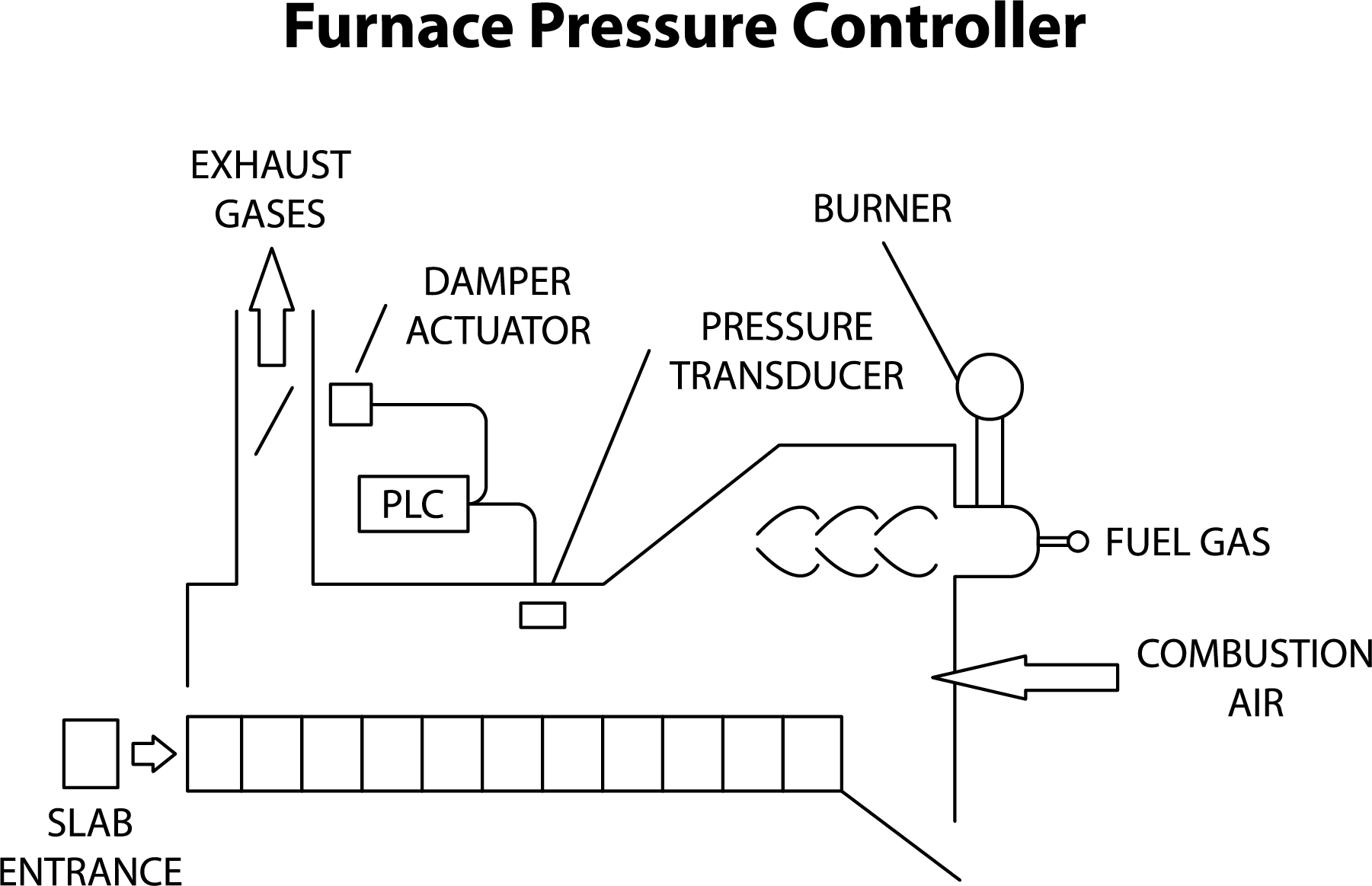
of thin sheet metal but consume significant amounts of energy – particularly with reheat furnaces. These furnaces are gas fuel energy intensive, second only to blast furnaces.
The reheat furnace is located at the hot strip mill and is the process step before hot rolling. In this step, steel billets, plates or blocks are usually heated from room temperature to ~1,200 C°. At this temperature, the billet can be hot rolled and achieve the desired metallurgical, mechanical and dimensional properties of hot rolled products. Optimal operation requires the minimization of fuel consumption, while maintaining a controlled steel billet thermal soak.
From economic, production and environmental standpoints, the operation of reheating furnaces is of great importance to the steel making process. Economically, the consumption of fuel needed for reheating can represent up to 15% of the operational cost of a rolling process. With respect to productivity, a reheat furnace capacity often dictates the production rate for the rollers, which means that reheating is usually the bottleneck in achieving the maximum production volume. The furnace operation must be reliable, as any down time will cost the average sized mini mill nearly $45,000 per hour in lost product revenue.
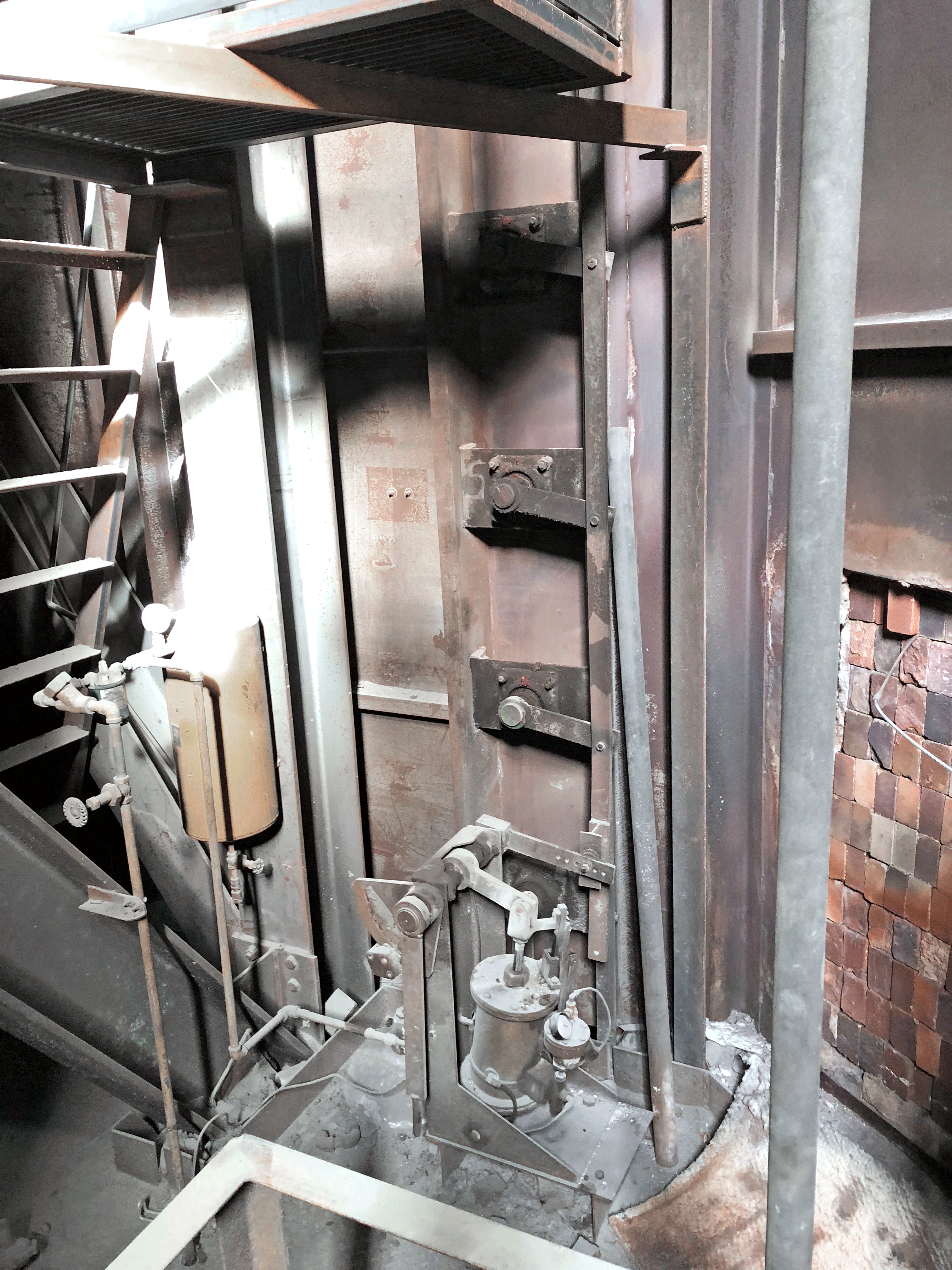
Maintaining a controlled ramp up and holding soak temperature is not a straightforward task. Heat transfer to the steel billets is influenced by internal temperature setpoint of the furnace, flow rate of fuels and flow rate of air. Maintaining furnace pressure is very important. If the furnace pressure is too low, air will ingress in the furnace with oxygen potentially causing scale formation, impacting quality and productivity. If the furnace operates too high, then the fuel consumption will increase operational cost.
At a steel mill in northeast Pennsylvania, the rolling mill team was frustrated by the furnace pressure control. The stack damper position used a pneumatic actuator and was responsible for the amount of flue gas exiting the stack. Control was poor and the actuator was not reliable. The unit required maintenance to recalibrate the position switches. In the winter, water in the air lines would freeze, making the actuator inoperable.
Success!
In 2019, REXA installed an Electraulic™ Linear actuator. The actuator immediately reduced the pressure setpoint by 38%, while furnace combustion efficiency improved without going into a vacuum condition. In addition, reduced fuel gas consumption saved the mill about $103,000 per year. The payback for the equipment investment was less than four months.
Check out the chart below detailing the old pneumatic actuator’s setpoint and our actuator’s setpoint. You’ll notice our actuator enabled a lower operating pressure right around the target setpoint, improving productivity.
Click the button below to learn more about our solution for other metals processing-related applications!
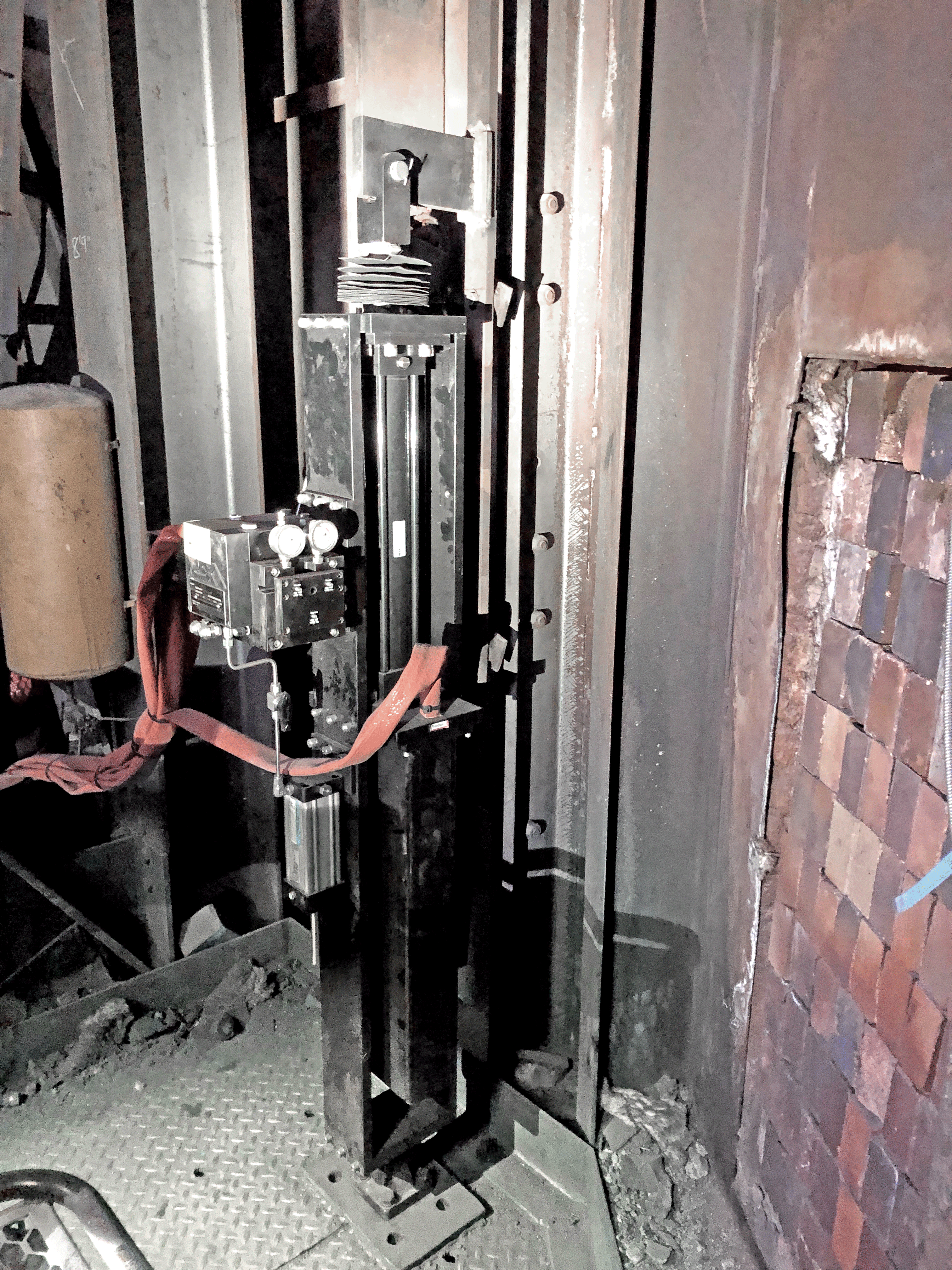
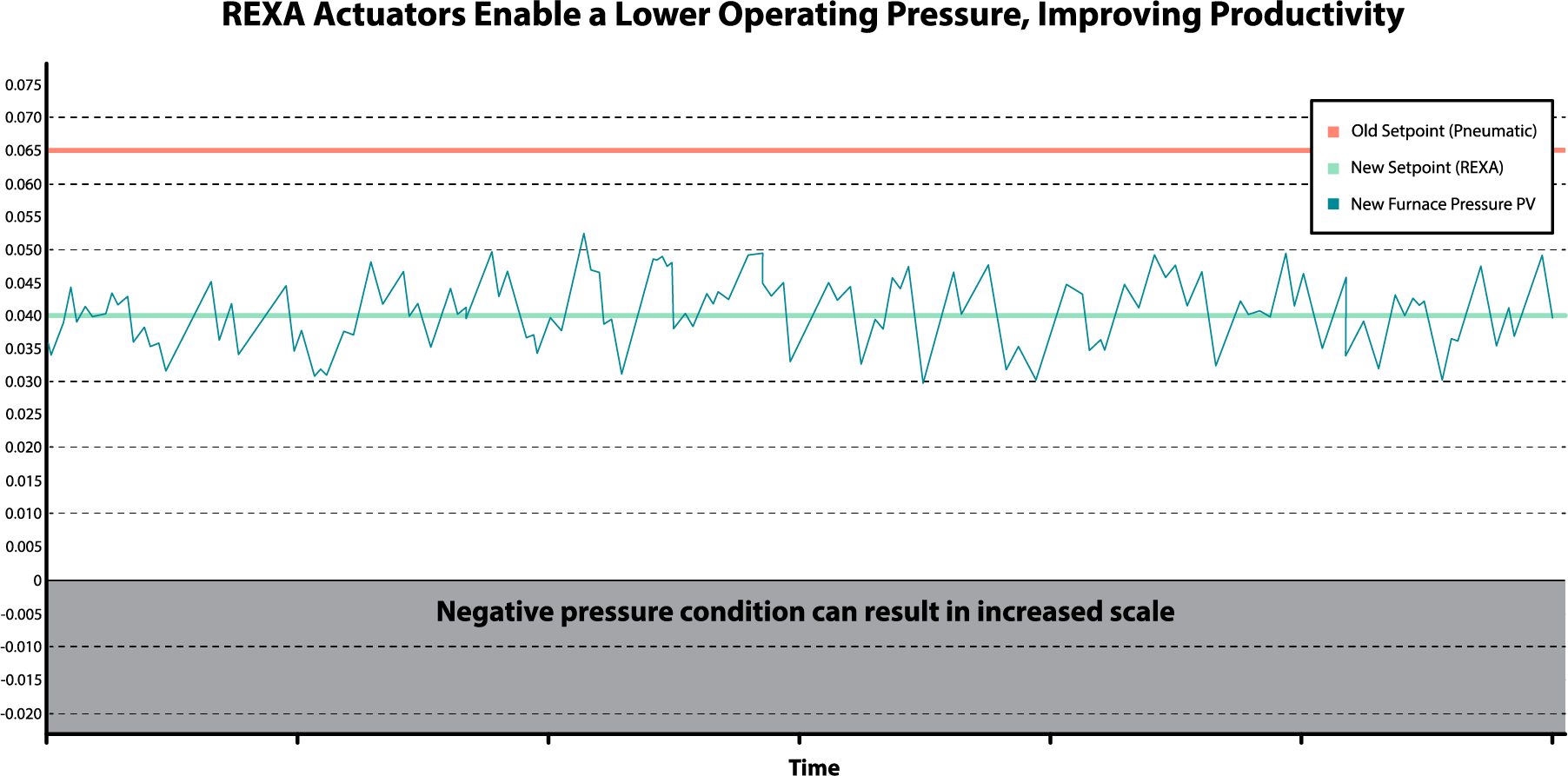