This article was published in OGN’s magazine and on OGN’s website. Click here to view the full-page spread!
REXA Actuators Chosen for Turnaround Project
Sabic Agri-Nutrients, a SABIC affiliate approached REXA last year in April exploring actuator solutions to upgrade two motor operated valves (MOV) to emergency shutdown valves (ESD).
According to SABIC Agri-Nutrients, the process licensor, KBR, suggested pneumatic actuators in place of the motor operated ones to achieve the fail-safe functionality required. Considering several challenges which needed to be overcome, SABIC decided to take a more in-depth approach.
The two valves, class 1500 16-inch and 14-inch ball valves, needed to be butt welded into existing pipework.
‘High pressure metal seated ball valves like these require a lot of torque to open/close especially considering safety factors. High output pneumatic spring fail actuators consist of large pistons and spring packs making the actuators very heavy and bulky. While the increase in weight and size can usually be accommodated in new build scenarios, it presents a significant challenge in an existing plant where the space envelope and pipe supports are already defined,’ Ali Khan, Aftermarket Service and Sales Engineer in Saudi Arabia, tells OGN.
‘Looking at this application from a process safety point of view, the valves need to close in less than three seconds under emergency conditions. Again, pneumatic actuators are capable of fast closing speeds but require additional dump valves and accessories, adding a layer of complexity to the installation; not to mention the need to install instrument air supply lines all the way to the valves,’ says Khan.
Finally, from a project perspective, these actuators were identified as the critical path for the turnaround and it was essential that all the functional requirements were
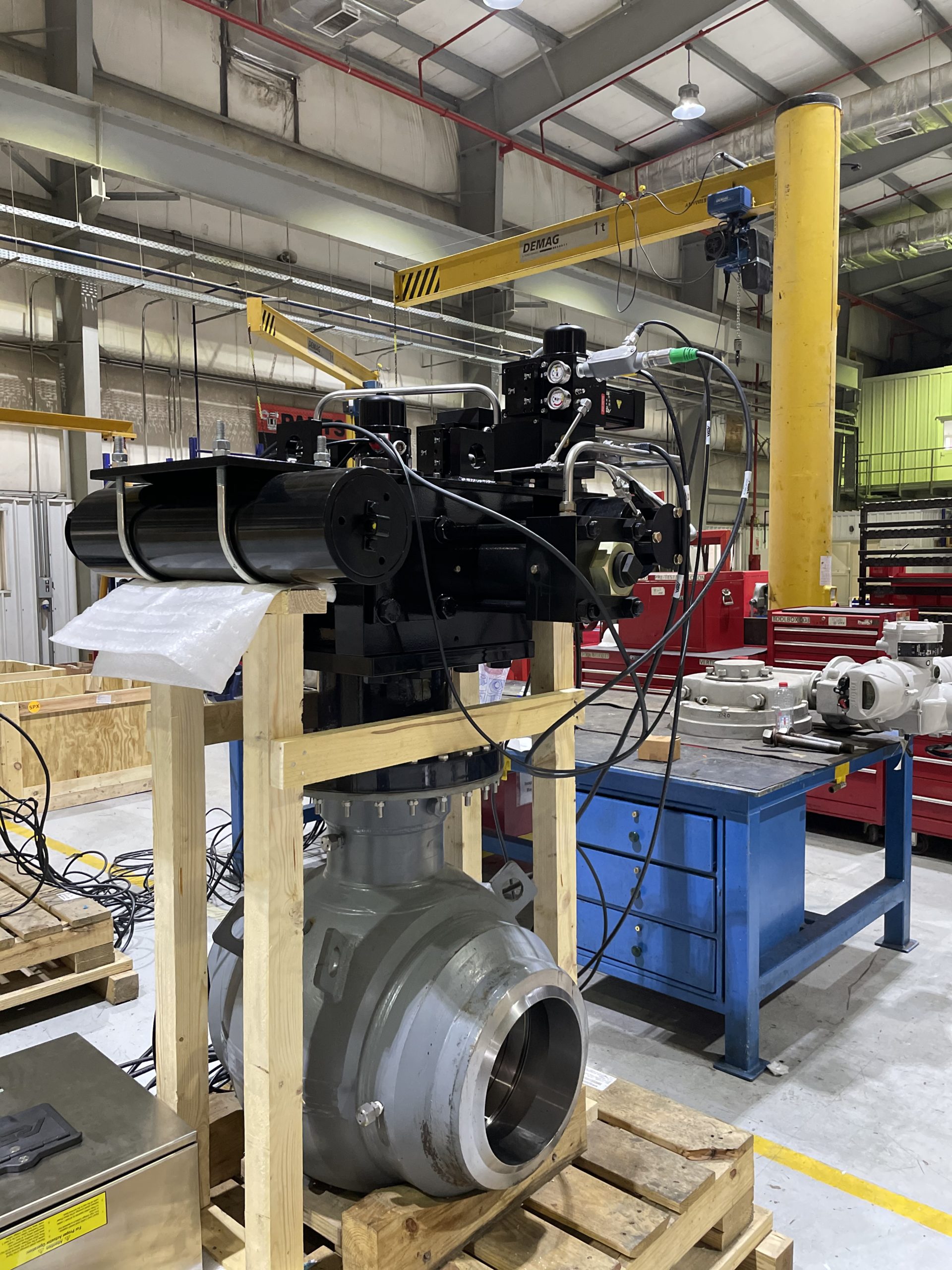
met with a reliable solution delivered to site within 15 weeks from order placement (industry standard is 18–24 weeks excluding shipment). The existing motor operated actuators would be removed, and the valves integrated with the new actuators in Saudi Arabia, and fully tested off-site before being taken back and welded into the pipeline.
Khan says: ‘Having worked closely together, a clear understanding of the myriad of challenges SABIC were facing was captured and REXA set about engineering a solution to check all the boxes.’
REXA’s Electraulic™ Actuation is a hybrid of hydraulic and electric actuator technologies utilizing a unique flow match valve (FMV) system. The FMVs allow an electrical motor to transfer a small amount of synthetic oil between two sides of a double acting hydraulic cylinder resulting in valve motion. Continuous motor operation is not required to maintain a position. On average, a REXA actuator contains 95 per cent less oil than a more traditional electro-hydraulic offering.
Equally important is the fact that REXA’s system does not require any regular oil maintenance or contain components which are subject to wear and regular replacement. The system contains no filters or externally vented reservoirs. Every segment of the hydraulic circuit is positive pressure, preventing contamination ingress and ensuring long-term oil cleanliness.
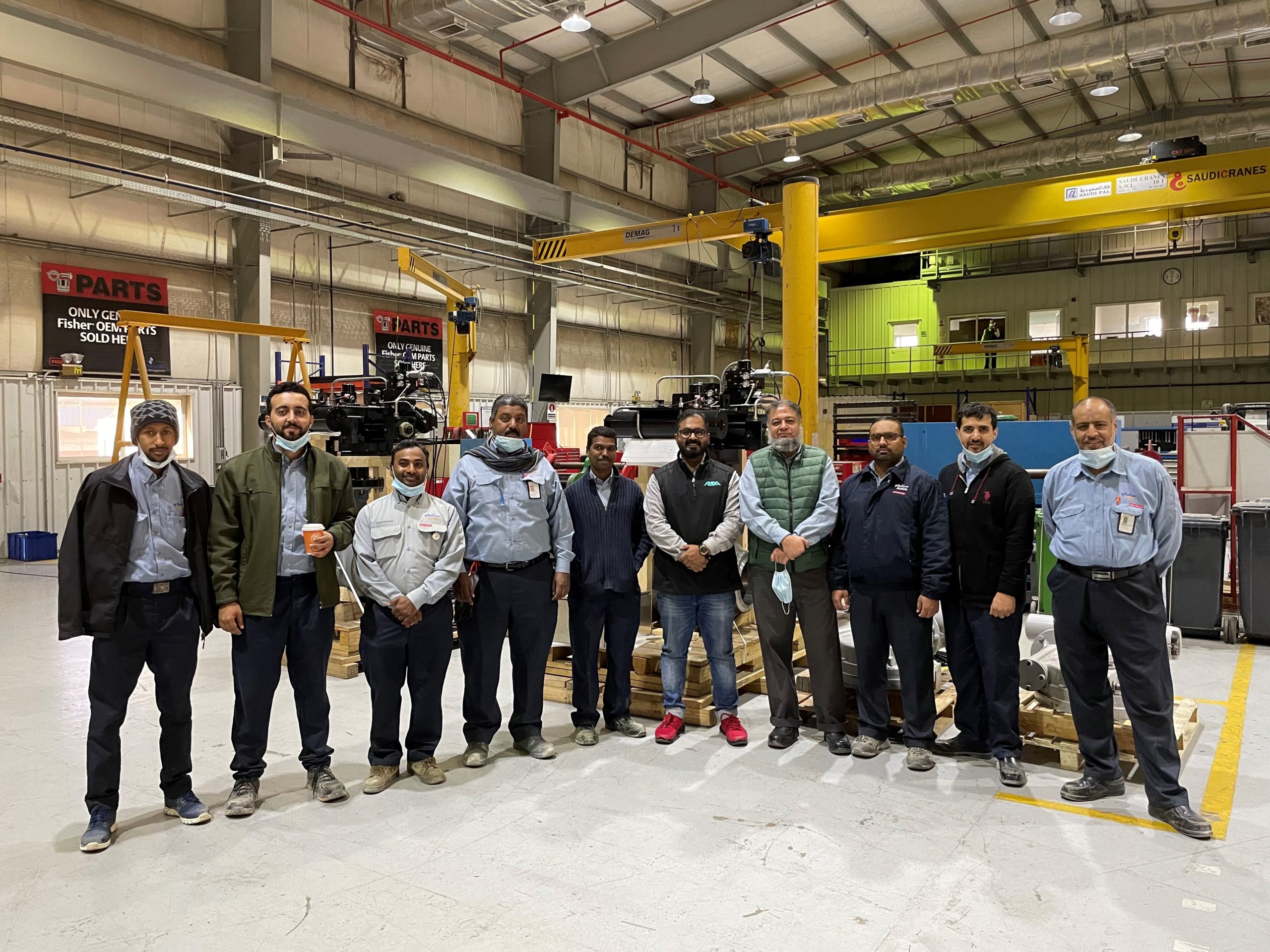
The existing electrical supply was considered and incorporated into REXA’s design. This removed the scope of work related to air supply lines and the need for expensive on-site electrical modifications.
Utilizing REXA’s experience, an accumulator centered system was chosen for fail-safe functionality, minimizing the complexity, physical size, and weight of the overall solution without compromising reliability or emergency closing speed.
Both actuators were delivered to REXA’s local representative’s premises in Jubail for mounting and a witnessed Factory Acceptance Test (FAT), which met the aggressive project schedule.
The actuators consistently achieved 1.5 seconds emergency closing speed during the comprehensive testing program.
‘SABIC could easily have taken the road so well-travelled and chosen off the shelf commodity pneumatic actuators. If any one of project specific requirements were missed, it would have resulted in significant delays, hidden costs in the form of site works and modifications or lost production time. But due to SABIC’s astute approach and close co-operation with an experienced actuator OEM utilizing unique technology, all the deliverables were met on time and within budget,’ concludes Khan.
Click below to learn more about our solutions for the Downstream O&G industry!